Cement level measurement in cement production is a complex task. Unlike liquids with their smooth, predictable surfaces, cement and other solid materials present a unique set of challenges. These challenges require innovative solutions to ensure accurate and reliable readings.
Dust, a common byproduct of cement production, is the most notorious obstacle to accurate cement level measurement. This fine particulate matter can cloud sensors and obstruct readings, much like trying to measure the depth of a fog-filled pool. However, dust isn’t the only challenge. The irregular surfaces of solid materials, ranging from fine powders to coarse clinker, can create uneven and unpredictable levels. Moreover, the immense tensile forces within tall silos can damage or even destroy traditional measurement tools.
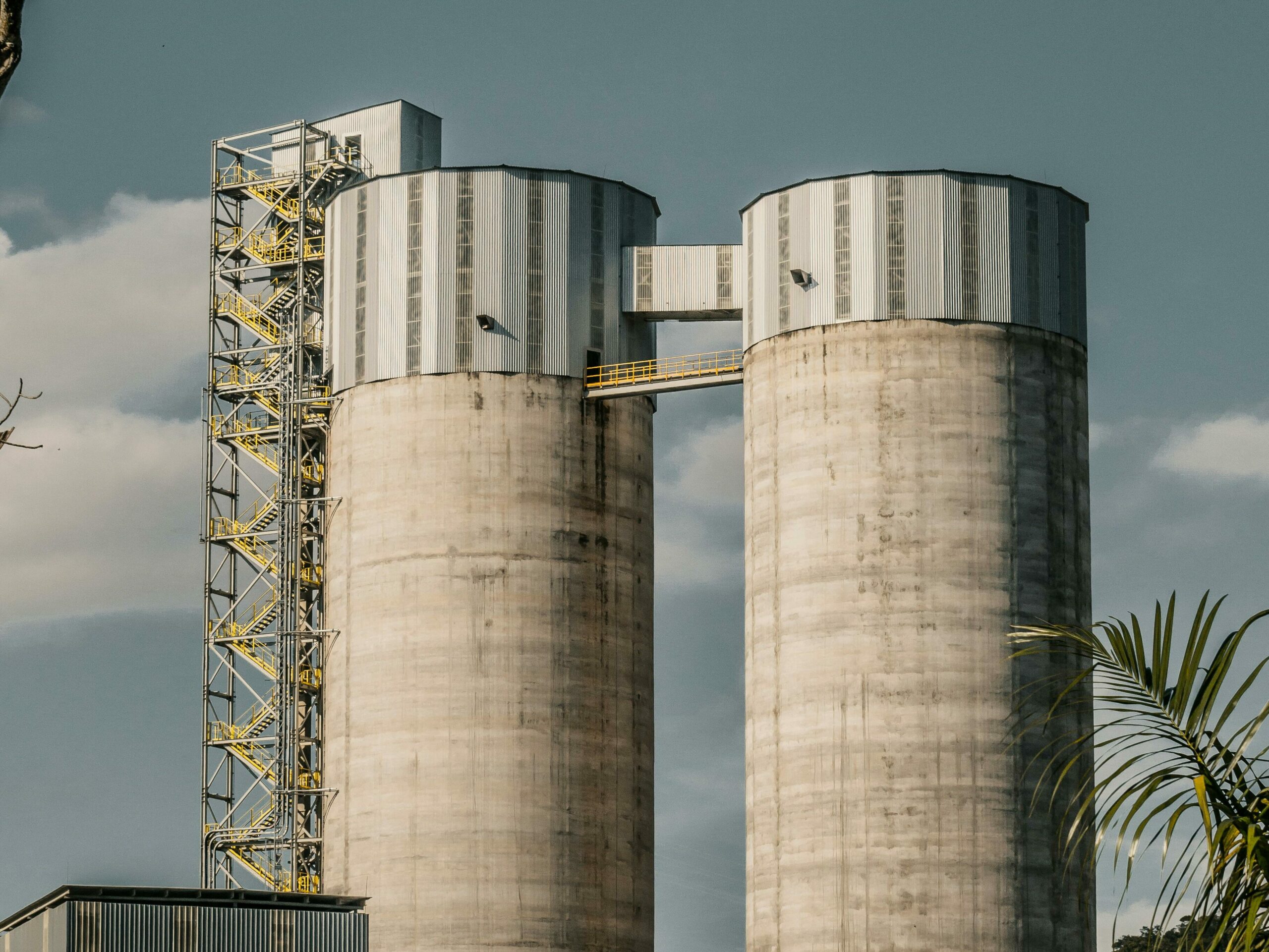
Historically, cement producers relied on manual measurements, a time-consuming and potentially hazardous process. Thankfully, technology has evolved to offer more efficient and safer solutions. Contacting devices like “Yo-Yos,” which lowered the weight of a cable to detect the material surface, were once the norm. However, these devices were prone to maintenance issues and could even damage downstream equipment if the cable snapped.
The advent of non-contacting level measurement technologies, such as radar, has revolutionized the industry. High-frequency radar, in particular, offers significant advantages for solids measurement. Its smaller antenna size and narrow beam angle make it ideal for navigating the challenges of dust and irregular surfaces in cement silos.
Radar sensors excel in the harsh environment of cement production. They can handle dust, varying surface dynamics, and withstand the strong tensile forces found in tall silos. The narrow beam angle of high-frequency radar also minimizes interference from internal obstructions like ladders and fill streams, ensuring accurate cement level measurement.
The advantages of high-frequency radar for cement level measurement are numerous. It provides precise readings even in challenging conditions. Its non-contacting nature reduces the need for maintenance due to fewer moving parts and less wear and tear. Furthermore, it eliminates the need for workers to climb silos for manual measurements, enhancing worker safety. The real-time data provided by radar sensors allows for better process control and optimization, leading to increased efficiency.
As technology continues to advance, we can anticipate even more sophisticated cement level measurement solutions. These advancements will further improve efficiency, reduce downtime, and enhance worker safety.
In conclusion, while level measurement in cement production presents unique challenges, it’s not an insurmountable problem. By embracing modern technologies like high-frequency radar, you can overcome these obstacles and achieve accurate, reliable cement level measurements that drive your operations forward.
You can explore another informative article on our website.
Source: Siemens